Rigid-flex circuit boards (PCBs) are crucial components in a wide variety of industries because of their unique properties. At their core, they are a combination of hard-printed circuit boards connected by flexible circuitry, which gives the final product a high degree of customizability and resistance to a variety of environmental extremes. All Flex Solutions is a manufacturer of various PCB applications.
Because of their unique properties, rigid-flex PCB applications are vast, spanning numerous industries, including military, aerospace, medical electronics, and more. They are important to these sectors because of their flexibility, versatility, and required use in never-fail electronics.
This article covers the advantages of rigid-flex boards and the most popular rigid-flex PCB applications, such as medical device and aerospace PCBs.
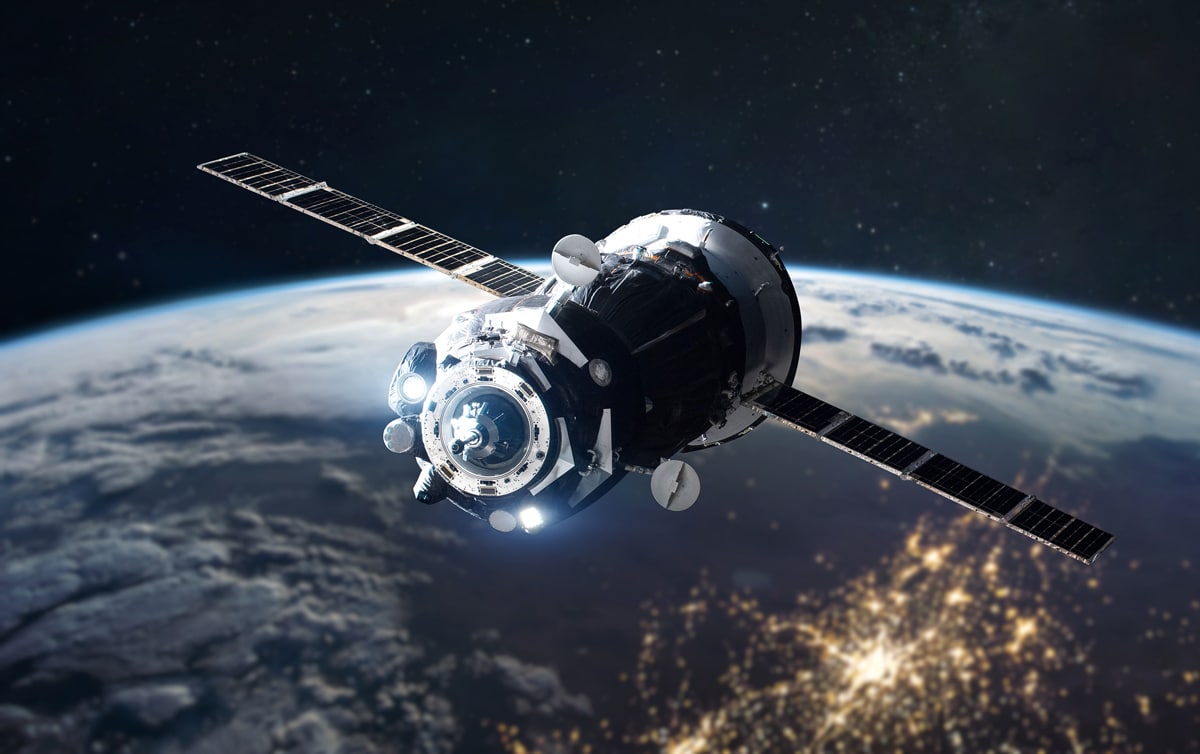
Advantages of Rigid-Flex Circuit Boards
Designing products with rigid-flex PCB offers you several advantages as an engineer. As the demands for smaller and more technologically integrated products increase, so does the use case for rigid-flex PCB applications.
Rigid-flex circuit boards allow designers to design solutions around a single PCB assembly and reduce the number of interconnecting cables, which is often a weakness of electronic designs.
Rigid-flex PCB applications also allow other design considerations, as fitting these PCBs into and around smaller spaces is easier. They can fit in tighter spaces because rigid-flex printed circuit boards can flex into and around curved areas. Additionally, rigid-flex PCB assemblies can layer over each other to take up less space along the X or Z axis.
In addition to being easier to design to fit specific spaces, the continuous electrical connection between the rigid and flexible sections reduces connection issues and increases input/output connectivity. Although these types of PCBs feature a somewhat complex development process, with considerations for total flexibility, operational integrity, and layered materials, they are a very cost-effective solution compared to other methods of connecting hard boards. It’s hard to match the reliability of rigid-flex PCB applications as well. These boards are specially designed to meet the needs of many high-stress industries, including military, medical, and aerospace equipment. Because these assemblies have some flexibility built in, they are incredibly vibration-resistant, and their construction components ensure they are resilient against other harsh factors such as extreme temperature. In cases where they integrate as part of a flexible heater assembly, they can also withstand exposure to potentially corrosive materials when used in an encapsulated assembly.
Weight reduction is another aspect that is considered at every step of the design process, including circuit design, in some specific use cases, especially in the aerospace and wearables markets. Rigid-flex PCB applications are an excellent way to help reduce the overall weight of your product designs since portions of the circuitry aren’t tied to hardboard, a heavier material than flexible circuits.
Best Use-Cases for Rigid-Flex Circuit Boards
Many popular products rely on rigid-flex PCB applications to design better products and ensure long-term operability in never-fail components. Many items you rely on today are already using rigid-flex components.
Consumer Devices
Due to the increasing demand for smaller devices, many products now use rigid-flex PCBs to meet these design expectations. Consumer devices such as smartphones and digital cameras all rely on rigid-flex PCBs. For example, a DSLR camera PCB board has several components on a relatively awkward body shape. Many modern cameras feature a touchscreen, buttons for various settings, shooting presets, manual shooting settings, light sensors, and motors. These all communicate through a camera PCB board to work as intended.
Medical Devices
Medical devices, especially those with never-fail componentry, rely on rigid-flex PCB applications. Pacemakers, various implants, and portable diagnostics equipment all use PCB designs for medical devices. Because these devices aren’t easy to maintain or replace, they must have the lasting dependability that rigid-flex PCB applications provide.
Automotive Components
Like modern cameras, the automotive industry increasingly uses electronic components. Components such as driver assistance systems, entertainment consoles, electronic control units, and others benefit from rigid-flex PCB assemblies. A rigid-flex PCB is a great way to account for this because vehicles potentially expose components to higher-than-normal amounts of vibration or heat.
Wearable Tech
Wearable technology is light, compact, and equipped with complex electronics that handle many tasks, such as internet / Bluetooth connectivity, heart rate monitoring, and more. Consumers expect these devices to be light and ergonomic as well, making them an excellent candidate for rigid-flex PCB applications.
Automotive Components
Industrial manufacturing machinery is complex and relies on rigid-flex circuitry to carry out repetitive tasks thousands of times without fail. Traditional wired connections between hardboards are more likely to become loose or fail, meaning the machine goes down until it can be repaired, costing businesses money. Rigid-flex PCB applications on industrial components ensure machines have less downtime due to these issues, allowing them longer operational lifespans.
Industries Using Rigid-Flex Circuit Boards
Today, many industries rely on the use of rigid-flex circuit boards for their durability, flexibility, and workability in tight or complex spaces. These industries include, but aren’t limited to:
Military and Aerospace
Military PCB and aerospace PCB applications are often needed for settings with high-reliability requirements. These products must work under extreme conditions such as high vibration, heat, mechanical stress, and more to keep troops safe and ensure that aerospace equipment works functionally.
Medical Devices
In the aerospace industry, durability, flexibility, and lower weight are all important design considerations for why rigid-flex is used in aerospace PCB assembly. Navigation consoles and other control mechanisms rely on the dependability of rigid-flex PCB applications.
Camera Industry
The camera industry relies on rigid-flex PCB applications to provide working functionality for camera bodies with many complicated inputs and toggles. Modern DSLR and mirrorless cameras operate with a high integration volume between small electronics clusters.
Satellite Applications
Some PCB assembly components are part of never-fail applications, such as satellites and other devices that are impossible to replace. Because satellites must operate perfectly without any manual routine maintenance, their durability, and long-term operability are crucial to their design and deployment process.
Telecommunications Industry
The telecommunications industry relies on rigid-flex PCB applications for several components such as base stations, tower antenna, and other communication devices. Rigid-flex PCBs offer better signal transmission and better connectivity than other solutions.
Still unsure if rigid-flex PCB applications are right for your engineering task? Give us a call or contact us to request a quote or a design consultation, during which we can discuss the possibilities of custom rigid-flex circuits on your project. All Flex Solutions is a leader in flexible componentry manufacturing and design.