Explore the latest innovations in PCB aerospace manufacturing, from miniaturization techniques to advanced materials that reduce weight.
Weight reduction is a top priority in PCB aerospace design. Every gram matters when it comes to fuel efficiency, performance, and compliance with strict industry standards. But reducing weight without sacrificing functionality is a challenge – especially in avionics systems that demand high reliability.
This blog by All Flex Solutions will explain how you can use rigid-flex PCBs – a lightweight alternative – to enhance fuel efficiency while maintaining top-tier performance. You’ll also learn about miniaturization techniques and material innovations that make rigid-flex the go-to choice for aerospace applications.
Your content goes here. Edit or remove this text inline or in the module Content settings. You can also style every aspect of this content in the module Design settings and even apply custom CSS to this text in the module Advanced settings.
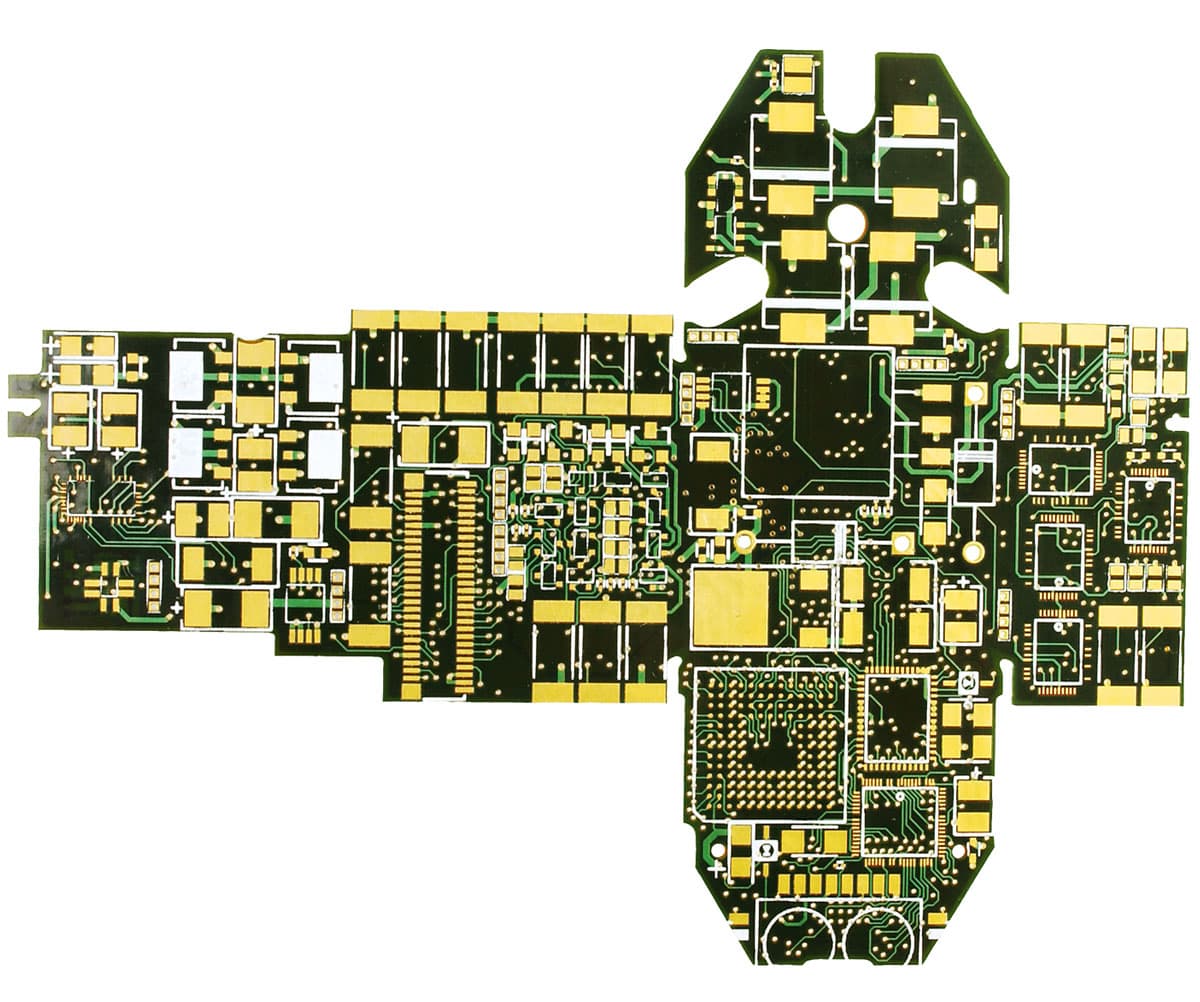
Why Weight Reduction Matters in PCB Aerospace Design
Every component in an aircraft contributes to fuel consumption, and even small weight savings can lead to significant efficiency gains. Here are three key reasons to reduce weight:
- Fuel Efficiency: Lighter PCBs reduce the overall weight of avionics systems, resulting in lower fuel consumption and operational costs.
- Structural and Thermal Constraints: In aerospace applications, PCBs must withstand extreme conditions without adding unnecessary weight. Materials need to be both durable and lightweight to ensure reliability.
- Miniaturization Demand: The industry is shifting toward more compact, high-performance avionics. Engineers are constantly looking for ways to integrate more functionality into smaller, lighter designs.
The Lightweight Alternative
PCBs with rigid strength yet flexible connectivity are a smarter, lighter alternative to traditional designs. Three key benefits make them ideal for aerospace applications:
- Weight Savings – By eliminating connectors and cables that consume PCB real estate and weight, strong and flexible rigid flex PCBs significantly reduce overall system weight. Fewer components mean a streamlined design with improved reliability.
- Improved Reliability – Fewer interconnects mean fewer potential failure points. This is critical in high-vibration aerospace environments where durability is non-negotiable.
- Flexible Design Options – Rigid-flex technology allows for compact, space-saving configurations. Engineers can optimize avionics layouts without compromising on performance.
Miniaturization Techniques in PCB Aerospace Design
As aerospace technology evolves, the demand for smaller, more efficient PCBs continues to grow. Engineers use miniaturization techniques like the ones below to maximize functionality while reducing weight:
- High-Density Interconnect (HDI) PCBs – HDI technology optimizes space by using finer traces, microvias, and multiple layers to pack more capability into a smaller area.
- Embedded Components – By integrating resistors and capacitors directly into the PCB layers, you reduce the need for bulky surface-mounted parts.
- Advanced Circuit Layering – Multiple layers of PCBs made with rigid-flex technology and very thin layers allow for complex circuitry within a compact, very lightweight footprint.
Material Innovations
By leveraging innovative materials, you can create high-performance, lightweight PCBs that meet the rigorous demands of aerospace applications. Here are some to consider:
- Polyimide Substrates – Known for their lightweight yet strong properties, polyimide materials provide flexibility and resilience.
- Flexible Adhesives and Coatings – Protective coatings shield PCBs from moisture, chemicals, and extreme temperatures.
PCB Aerospace Design with All Flex
PCB aerospace design means eliminating bulky connectors, integrating miniaturization techniques, and leveraging advanced materials. In doing so, engineers can create lighter, more efficient avionics systems without compromising functionality.
Optimize your aerospace PCB manufacturing designs with All-Flex’s rigid-flex technology.