Rigid Flex PCB Solutions with All Flex
Design Your Custom Rigid Flex PCB
All Flex Solutions is the leading manufacturer of custom-built rigid flex PCBs. Rigid flex circuit boards offer the best in packaging technology by merging the flexibility of flex circuits with the dense packaging of traditional rigid circuit boards. Ideal for high shock and high-vibration applications, design confidently with All Flex. Ready to design your custom Rigid Flex PCB?
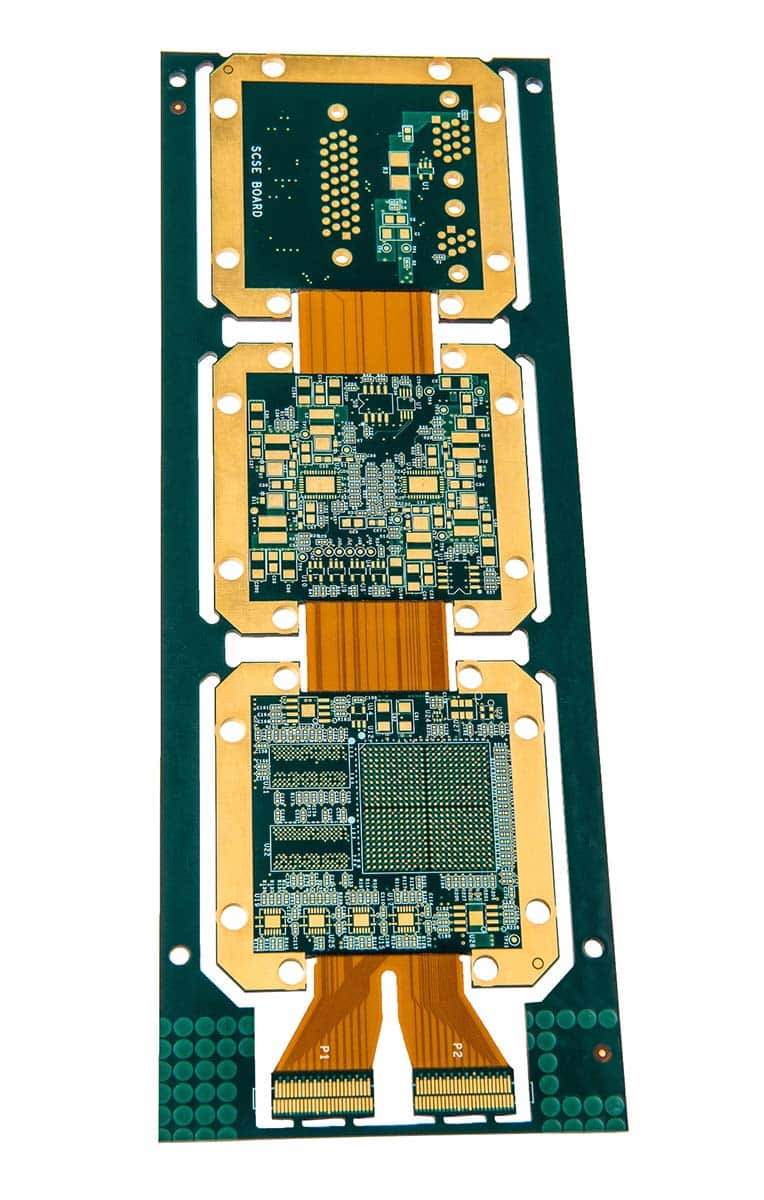
What is a Rigid Flex PCB?
Rigid flex printed circuit boards (PCBs) provide designers with one of the more unique packaging methods for electronic designs. Combining the component and routing density of hardboards with the flexibility of flexible circuits, rigid flex PCBs allow designers to achieve routing density and interconnectivity that is not available in other types of circuit boards.
Primarily used in military, medical and camera applications, rigid flex PCBs comprise about 1% of the overall PCB market, but they are increasingly used in other electronic applications. They cost more than traditional PCBs due to the raw materials required; but, in the right applications, rigid flex PCBs dramatically outperform traditional circuit boards, and they can be more cost-effective in a full solution.
Benefits of a Rigid Flex PCB
All Flex rigid flex PCBs are manufactured with very high reliability rolled annealed copper foil for “flex to install” or dynamic flex applications with hundreds of thousands of flex cycles without electronic failure.
The flexible layers are buried within the rigid flex PCB, differing from surface-mounted connectors and flex cables which can fail. Like flex circuits, the flexible sections of a rigid flex board have “dynamic flex” capabilities, i.e. the ability to withstand hundreds of thousands of flex cycles without breaking.
Valu Build Program: Create a Custom Rigid Flex PCB
All Flex Solution’s ‘Valu Build’ Program provides the customer with very stable and robust rigid flex solutions at the lowest possible cost. For the right applications, this makes all the difference.
In projects with four or more interconnected hard boards, rigid flex circuits can provide a more cost-effective solution than the combined assembly.
- Very thin dielectrics make rigid flex circuits ideal for weight saving applications, like drones, unmanned vehicles, aerospace, and space applications.
- Rigid flex is unsurpassed in high vibration environments. In vibration testing rigid flex PCBs will survive even when staked and soldered components fail.
- Rigid flex is unsurpassed in high shock applications of 10,000+ G-forces in which traditional PCB packaging would fail.
When Should You Use Rigid Flex PCBs?
- When a designer needs a flexible solution & needs to rout components on both sides of the PCB
- When a designer requires electronics fit the device, rather than the device conform to the electronics
- When the electronic components & connectivity required max out space for connectors & flex cables
- As a single-package solution for electronics with high input/output connectivity
- As a cost-effective alternative to a combined assembly of interconnected hard boards
- When the designer has to miniaturize their design to accommodate greater functionality
- In weight-saving applications, such as drones, unmanned vehicles, aerospace & space applications
- High vibration environments
- High shock applications – where electronics will be subjected to 10,000+0 G-s
- In never-fail electronics
Rigid Flex PCB Features
- Available in layer counts above 20 layers for very high routing density
- Flexible layers typically 1, 2, 3 or 4, though more can be accommodated
- Controlled impedance in both rigid & flexible sections
- Very high reliability
- Minimum dielectrics: down to 1 mil in flex sections, 2 mil in rigid sections
- Largest library of rigid flex constructions approved to UL 94 V-0
- RoHS compliant
History of High Reliability Rigid Flex Circuits
Rigid flex PCBs started gaining a wider market through the 1990s. Medical device designers wanted high reliability packages in tiny formats for products such as pacemakers, defibrillators, and cochlear hearing implants. Rigid flex PCB technology allowed for both miniaturization and improved reliability.
In 1997 All Flex committed their resources to rigid flex PCBs, spending the following decades investing in the equipment and processes to excel in advancing this technology and delivering it to broader markets.
Custom Development
Ready to begin designing your custom Rigid Flex circuit? Give us a call to request a quote or a design consultation, or download our free design guide today!